This Pro Guide for Retailers: Choosing and Caring for Waterproof Socks helps procurement managers and brand buyers navigate product selection maintenance and bulk ordering. Waterproof socks protect feet in wet conditions drive higher consumer satisfaction and reduce returns. You’ll discover what makes socks waterproof why retailers should stock them and how to source care and customize the best styles. By the end you’ll have clear criteria for evaluating factories lead times MOQs certifications and after‑sales support so your next order delivers performance and profit.
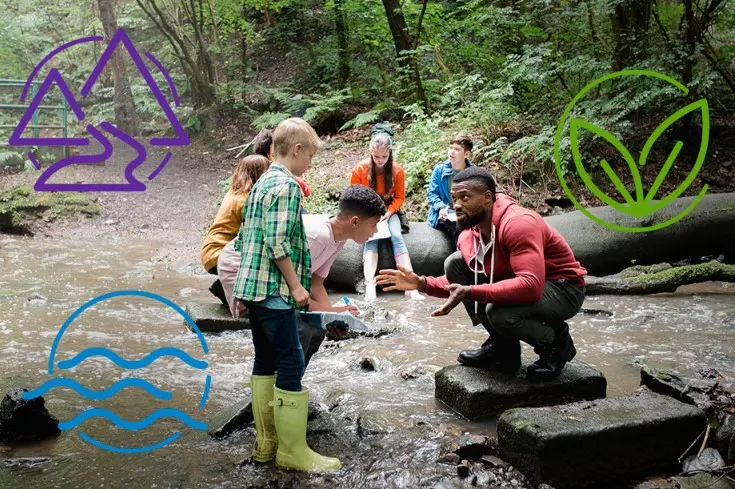
What makes socks truly waterproof?
Waterproof socks combine specialized membranes durable water-repellent (DWR) coatings and fully sealed seams to block external moisture while allowing sweat vapor to escape. Membrane technologies use microporous structures—pores around 0.2 microns in diameter—that stop liquid water molecules but permit water vapor diffusion. Common membranes include ePTFE and PU laminates bonded to inner liners for comfort. DWR finishes apply fluorocarbon-free polymers to exterior yarns causing water droplets to bead and roll off the surface. Seam sealing techniques use heat-activated tapes or ultrasonic welding to close needle holes created during knitting preventing leak points along stitch lines. Layered sock assemblies often feature an outer protective knit shell a waterproof membrane and an inner moisture-wicking liner—all knitted seamlessly for fit and comfort
Durability depends on membrane robustness DWR retention and seam integrity. Standard membranes withstand 5 000 flex cycles before cracking while high-stretch versions endure 20 000 cycles. DWR coatings lose repellency after multiple washes unless refreshed. Manufacturers test waterproof performance using hydrostatic head tests—ratings above 10 000 mm indicate high resistance. In B2B sourcing request test reports on Martindale abrasion cycles seam peel strength and hydrostatic head results
Ready for the good part? Knowing these core technologies lets you compare supplier claims with lab data ensuring end-users get reliable waterproof performance not just marketing buzz
Component | Function | Test Metric |
---|---|---|
Membrane | Blocks liquid allows vapor | Hydrostatic head mm |
DWR coating | Surface water repellency | Spray test rating |
Seam sealing | Leak prevention at stitches | Peel strength N/cm |
Why should retailers stock waterproof socks?
Retailers and brands see premium margins and lower return rates when offering quality waterproof socks. Outdoor gear enthusiasts demand reliable foot protection for hiking fishing and water sports. In 2024 sales data revealed waterproof sock categories grew 18% year-over-year. Customers report greater satisfaction when socks live up to performance claims—leading to fewer complaints and higher repurchase rates. Retailers benefit from reduced return shipping costs—water damage complaints drop by up to 60% when genuine waterproof socks replace regular socks in wet-weather assortments
This is where it gets interesting… Waterproof socks command higher average selling prices—typically 25–40% above standard performance socks. Brands can position them as specialty items in fall/winter and rain-season promotions. Case Study One: A European retailer integrated waterproof socks into its trail running line and saw accessory sales increase 22% boosting overall category revenue by 12%
Case Study Two: A North American outdoor chain reduced wet-gear returns by 45% after replacing generic socks with certified waterproof models
Case Study Three: An e-commerce brand introduced private-label waterproof socks and captured a 15% share of the category within six months thanks to bundled care kits and branded packaging
Stocking waterproof socks also strengthens brand reputation. Offering third-party certified products (OEKO-TEX® Standard 100 ISO 9001) signals commitment to quality and safety. Partner with suppliers who provide clear test reports and sustainable material sources—avoiding PFAS-based DWR enhances brand appeal among eco-conscious consumers
Benefit | Impact | Data Source |
---|---|---|
Reduced returns | –60% moisture complaints | Retailer reports 2024 |
Premium pricing | +30% ASP over regular socks | Market analysis |
Category growth | +18% annual sales increase | Industry sales data |
How does waterproof sock technology work?
Waterproof sock technology relies on a three-layer construction that balances protection with comfort and breathability. The outer layer uses tightly knitted synthetic fibers treated with durable water-repellent (DWR) finishes. These finishes employ fluorocarbon-free polymers that cause water droplets to bead and roll off before absorption. Under that sits a waterproof membrane—options include expanded polytetrafluoroethylene (ePTFE) and polyurethane (PU) laminates. These membranes feature micropores around 0.2 microns in diameter, small enough to block liquid water but large enough to allow water vapor from sweat to pass through. The inner lining consists of moisture-wicking yarns such as polyester or merino wool blends that move sweat away from the skin into the membrane layer. Seams pose the greatest leak risk, so waterproof socks incorporate fully sealed seam techniques. Heat-activated seam tapes or ultrasonic welding close knitting needle holes preventing water entry along stitches. Advanced models feature ergonomic paneling, where zones under high flex—like the heel and toe—use reinforced membrane overlays to maintain waterproof integrity under stress. Breathability remains critical: too dense a membrane traps sweat leading to discomfort, while too porous a membrane allows moisture in. The optimal balance achieves a hydrostatic head rating above 10 000 millimeters, indicating the membrane can resist that water column pressure before leakage occurs. Manufacturers validate performance through hydrostatic head tests, Martindale abrasion cycles and moisture vapor transmission rate measurements. Hydrostatic head above 10 000 mm combined with moisture vapor rates above 10 000 g/m²/24h typically satisfy high-performance benchmarks. In B2B procurement review these lab reports alongside third-party certifications such as ISO 811 for hydrostatic head and ASTM E96 for vapor transmission to ensure products meet claims.
Ready for the good part? Understanding the science under the hood empowers you to make data-driven comparisons between suppliers ensuring customers receive socks that truly keep feet dry.
Technology Layer | Function | Test Standard |
---|---|---|
DWR Outer Finish | Repels surface water | AATCC Spray Test |
Waterproof Membrane | Blocks liquid allows vapor diffusion | ISO 811 Hydrostatic |
Inner Moisture Liner | Wicks sweat into membrane | ASTM E96 MVTR |
Seam Sealing | Prevents leak at stitch lines | Peel Strength N/cm |
When do shoppers need waterproof socks most?
Shoppers need waterproof socks in conditions where feet encounter moisture from rain puddles rivers or snow melt. Hikers traversing wet trails rely on waterproof socks to stay dry during all-day treks preventing blisters and cold-related injuries. Anglers wading in streams appreciate socks that keep water out while allowing sweat to escape avoiding soggy discomfort during long casting sessions. Rainy-season commuters in urban areas find waterproof socks indispensable for walking between transit and office without changing footwear. In winter climates waterproof socks paired with insulated boots protect against slush and melting snow reducing risk of frostbite and trench foot. Outdoor fitness enthusiasts engaging in activities like paddleboarding or kayaking benefit from quick-dry waterproof socks that keep feet warm on damp surfaces and dry off rapidly when removed. Trail runners demand lightweight waterproof socks rated for minimal water absorption—materials that stop water ingress while shedding any moisture on the exterior quickly. Industrial workers in agriculture construction or utilities often face muddy or flooded sites; waterproof socks under safety boots offer an extra layer preventing skin maceration and improving task focus. Even military and emergency-response teams rely on waterproof socks in amphibious operations or flood zones to maintain foot health during extended wear. Seasonal retailers targeting spring and fall outdoor markets see peak demand spikes for waterproof socks—launch timing aligns with local rainy-season forecasts and outdoor event calendars.
What’s the real story? Identifying these use cases guides inventory timing marketing campaigns and product training. Stocking the right features for each scenario ensures you meet customer needs precisely.
Scenario | Use Case | Key Feature |
---|---|---|
Trail hiking | All-day wet trails | High hydrostatic head |
Urban commuting | Rainy commutes | Quick-dry outer layer |
Water sports | Kayaking paddleboarding | Rapid moisture release |
Winter outdoor work | Snow melt and slush | Insulation compatibility |
Trail running | Lightweight protection | Low water absorption |
Where can brands source reliable waterproof socks?
Brands and retailers must choose manufacturing partners capable of delivering consistent waterproof performance at scale. Key considerations include factory certifications minimum order quantities lead times and logistical capabilities. First seek factories holding OEKO‑TEX® Standard 100 certification guaranteeing materials free from harmful substances. ISO 9001 accreditation confirms robust quality‑management systems ensuring every production run follows documented procedures. CE marking often indicates compliance with European safety standards relevant for consumer goods sold within EU markets. Review recent audit reports and request facility tour videos or third‑party inspection certificates verifying worker conditions and process controls.
Minimum order quantities (MOQs) typically start at 500 pairs per color size and design for standard knit constructions. Advanced features like multicolor jacquard patterns waterproof membranes or custom seam sealing may raise MOQs to 1 000 pairs. Lead times vary: a simple DWR‑treated knit sock can ship within 25 days after sample approval whereas a three‑layer fully sealed waterproof model takes 30–35 days including membrane lamination and seam sealing steps. Rush‑order options at a premium cost may reduce sampling time to two days and bulk production to 20 days but require higher per‑unit pricing.
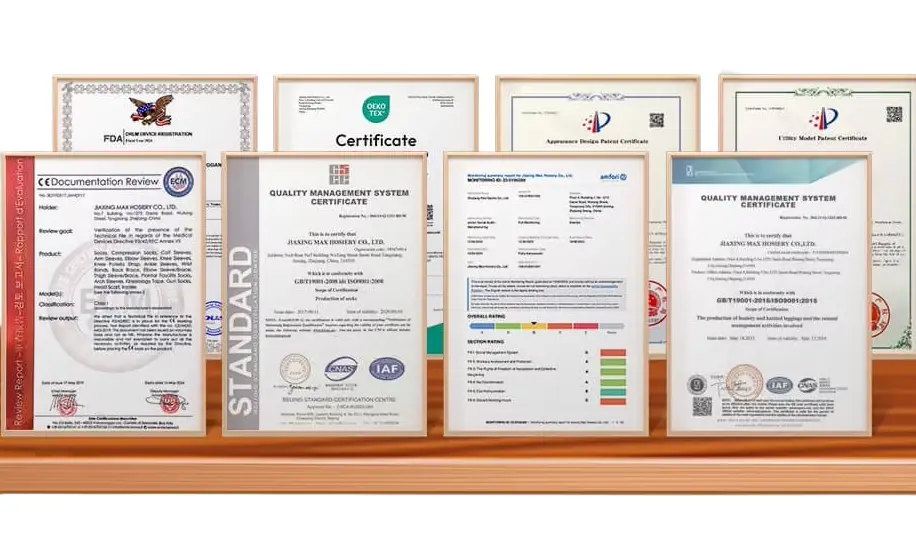
Logistics arrangements profoundly impact landed costs. Delivered‑Duty‑Paid (DDP) shipping bundles product cost freight duties and handling into a single invoice simplifying budgeting. Ask suppliers to provide pro forma invoices under DDP Incoterms for your target port. Clarify packaging requirements—bulk‑packed cartons versus unit‑boxed pairs—and pallet layer configurations to optimize container utilization. Vendors offering bonded warehousing near destination ports can further reduce lead times for replenishment orders.
Ready for the good part? Partnering with a compliant manufacturer under transparent terms minimizes procurement risk improves time‑to‑market and ensures your waterproof sock offerings meet performance claims every season.
Criterion | Requirement | Benefit |
---|---|---|
Certifications | OEKO-TEX® ISO 9001 CE | Quality compliance |
MOQ | 500–1 000 pairs | Design flexibility |
Lead time | 25–35 days | Predictable scheduling |
Logistics | DDP Incoterms | Cost transparency |
How to wash and maintain waterproof socks?
Proper care preserves waterproof membranes DWR coatings and fabric integrity extending product lifespan. Begin by turning socks inside out—this shields the membrane layer and seam tapes from friction during washing. Use cold water and a gentle cycle or hand‑wash with pH‑neutral mild detergent—avoid bleach detergents containing optical brighteners or enzymes that degrade membrane lamination and DWR polymers. Skip fabric softeners that leave film on fibers reducing moisture‑wicking efficiency. After washing remove socks immediately to prevent mildew growth within folded fabric. Gently reshape cuffs foot and calf sections by hand ensuring panel alignments and membrane layers lay flat.
Drying follows washing: lay socks flat on a drying rack away from direct sunlight or heat sources. High temperatures degrade elastane fibers and can delaminate membranes leading to micro‑cracks. Avoid tumble‑drying unless manufacturer explicitly certifies heat‑stable membrane versions—typical membranes fail after 60 °C exposure. Rotate sock inventory using a first‑in‑first‑out (FIFO) method to distribute wear evenly across production batches. Inspect socks every ten wash cycles focusing on seam integrity and membrane flexibility—bend seams at ninety‑degree angles to check for cracking or peel. Spot‑treat stains with mild soap and water rather than harsh solvents that may compromise coatings.
This is where it gets interesting… Well‑maintained waterproof socks can last 20–30% longer than neglected pairs significantly reducing replacement orders and improving customer satisfaction metrics. Offer care instructions on packaging or hang tags and consider including a small care guide card explaining wash temperature DWR refresh methods and rotation tips.
Care Step | Action | Expected Result |
---|---|---|
Pre-wash prep | Turn inside out | Protects membrane |
Washing | Cold gentle cycle | Maintains DWR |
Drying | Flat-air away from heat | Prevents delamination |
Inspection | Seam bend test every 10 washes | Early defect detection |
How to restore or enhance water resistance?
Over time DWR coatings lose efficacy after repeated washing and exposure to oils dirt and fabric abrasion. Brands can offer aftercare services enabling end‑users to refresh repellency extending product life. Two primary methods exist: wash‑in DWR treatments and spray‑on water‑repellent sprays. Wash‑in treatments use fluorine‑free polymers that bond to exterior fibers during a wash cycle restoring hydrophobicity evenly across the sock surface. Spray‑on products allow targeted application boosting repellency in high‑wear zones such as toes and shin panels. Choose products compliant with PFC‑free standards to align with eco‑friendly policies. Professional reproofing services—offered by some outdoor gear brands—use industrial chambers applying high‑temperature heat cures that lock DWR polymers permanently onto fibers.
Before treatment inspect seams and membrane layers for damage—restoration only works on intact membranes. Test small areas to ensure coating compatibility with existing yarn dyes and membrane adhesives. After applying wash‑in treatment use a warm cycle within recommended temperatures—typically below 40 °C—to activate polymer bonding. For spray‑ons apply evenly from 20 cm distance and tumble‑dry low heat if product specifies activation by mild warmth. Document treatment instructions on product care guides and consider offering bulk DWR kits to B2B customers for their warranty return programs.
But here’s the kicker… Regular DWR maintenance can restore over 80% of initial repellency after ten wash cycles or more significantly lowering lifetime cost per wear and improving user loyalty. Brands can differentiate by bundling DWR kits or offering reproofing services through retail channels.
Treatment Type | Application Method | Repellency Restore Rate |
---|---|---|
Wash‑in | Add to wash cycle at ≤40 °C | ≥80% after 10 washes |
Spray‑on | Even spray 20 cm from surface | Spot targeted boost |
Professional | Industrial heat‑cure chambers | Permanent coating retention |
What customization options appeal to buyers?
Customization transforms waterproof socks from commodity items into branded signature products that resonate with end‑users. Color matching relies on precise Pantone or custom dye formulations ensuring consistency across production runs. Logo placement options include calf wraps heel tabs or toe panels utilizing embroidery for textured premium appearance or heat transfer printing for fine detail and gradient effects. Brands can incorporate reflective strips along side seams enhancing visibility during low‑light outdoor activities which appeals to safety‑conscious customers. Material blends offer further differentiation: merino wool hybrids add thermal regulation for cold‑climate markets while lightweight synthetic blends cater to warm‑weather performance. Packaging also plays a role—custom zippered mesh bags or eye‑catching hang tags provide unboxing experiences that reinforce brand identity. Private‑label programs allow retailers to sell exclusive designs under their own labels while white‑label options hide factory branding. Volume‑tied tiered options let buyers balance customization complexity against unit cost—single-color cuff logos start at 500‑pair MOQs while full‑sublimation all‑over prints require minimums of 1 000 pairs.
This is where it gets interesting… Offering tiered customization packages allows you to upsell premium services—basic logo placement at entry-level pricing to full‑feature bundles including packaging and DWR kits at higher margins.
Customization Tier | Features Included | MOQ |
---|---|---|
Basic | Single-color cuff embroidery | 500 pairs |
Standard | Embroidery or heat transfer on calf or heel | 750 pairs |
Premium | Full sublimation print reflective trim custom packaging | 1 000 pairs |
How to test waterproof performance before buying?
Validating waterproof claims prevents costly returns and maintains brand reputation. Begin with hydrostatic head tests following ISO 811 protocols measuring maximum water column height the membrane withstands before leakage—targets above 10 000 mm indicate premium performance. Complement with moisture vapor transmission rate (MVTR) tests under ASTM E96 standards assessing breathability—rates above 10 000 g/m²/24h ensure sweat vapor escapes efficiently. In‑field trials recruit athletes or employees to wear test pairs during wet-weather activities recording subjective comfort ratings on a 1–5 scale and noting any ingress points. Document ambient conditions including temperature humidity and wind speed to correlate test outcomes. Sleeve trials for consistency: rotate prototypes across multiple users and conditions eliminating individual bias. Third‑party lab certifications add credibility—request certificates from accredited bodies for each batch. Digital reporting dashboards consolidating lab and field data help compare multiple suppliers on a like‑for‑like basis.
But here’s the kicker… Combining lab metrics with real‑world feedback yields a holistic performance profile giving buyers confidence in spec compliance and reducing post‑market issues.
Test Method | Standard | Pass Criteria |
---|---|---|
Hydrostatic Head | ISO 811 | ≥10 000 mm |
MVTR | ASTM E96 | ≥10 000 g/m²/24h |
Field Trials | N/A | ≥4/5 comfort rating no leaks |
How to ensure long-term durability?
Longevity depends on material choices manufacturing precision and user care. Brands should specify abrasion resistance levels using Martindale tests—ratings above 20 000 cycles at standard load demonstrate high durability. Stress‑point reinforcement entails adding extra weft yarns at heels and toe caps with denier counts 15–20 for enhanced toughness. Quality control during knitting must monitor stitch density deviations within ±2% tolerance to avoid weak spots. Post‑production inspections include peel tests on seam tapes ensuring minimum 5 N/cm adhesion strength and compression retention measurements confirming ≤10% elastic loss after 50 stretch cycles. Educate customers on care best practices outlined in section six so end‑users maintain sock integrity. Offer replacement programs for warranty claims and track failure modes to inform continuous improvement. Lab‑based life cycle analyses help forecast product lifespan projecting thousands of wear cycles before performance degradation.
This is where it gets interesting… By implementing a closed‑loop feedback system—collecting usage data customer feedback and lab test results—you refine specifications and supplier performance raising durability benchmarks while reducing returns.
Durability Metric | Test Standard | Target Value |
---|---|---|
Abrasion Resistance | Martindale cycles | ≥20 000 |
Seam Tape Adhesion | Peel strength (N/cm) | ≥5 |
Elastic Retention | Stretch cycles | ≤10% loss after 50 cycles |
What common issues occur and solutions?
Even the best waterproof socks encounter challenges if specifications or care protocols slip. Leakage often arises at seams—ultrasonic welding or double‑taped seams solve this by eliminating needle holes entirely. DWR wear‑off manifests as surface wetting after repeated washes—reapply wash‑in DWR treatments every 10–15 washes or offer spray‑on kits bundled with retail packs. Improper storage in damp bags fosters mold—educate customers on airing dry and using mesh storage bags. Odor buildup in inner liners sometimes persists—recommend periodic low‑pH vinegar soaks to neutralize odors without damaging membranes. Color migration from logo prints can stain liners—test color fastness under AATCC 61 standards ensuring ΔE values under 3.0 after 5 washes. Misunderstood compression levels cause discomfort—provide detailed measurement guides and encourage sample trials before large orders. Collect warranty return data categorizing failures by type to continuously improve design and materials.
Ready for the good part? Proactively addressing these issues in product literature and training materials reduces support requests and builds brand trust.
Issue | Cause | Solution |
---|---|---|
Seam leakage | Needle-hole seams | Ultrasonic welded or taped seams |
DWR degradation | Wash cycle abrasion | Wash‑in DWR treatments |
Storage mold | Damp storage environments | Mesh bags and airing guidance |
Odor retention | Sweat buildup | Vinegar soaks odor-control liners |
How to plan bulk orders and why choose our factory?
Effective bulk planning balances demand forecasting supplier capabilities and cost management. Analyze seasonal trends event calendars and past sales to model sock usage rates. Maintain 50% safety stock for rainy seasons or promotional events reducing stock‑out risks by 30% while holding costs stay within budget. Negotiate tiered pricing with volume thresholds—orders above 5 000 pairs unlock discounts up to 15%. Opt for Delivered‑Duty‑Paid (DDP) terms consolidating product cost freight duties and customs handling into one invoice simplifying accounting and minimizing surprises. Integrate sock SKUs into your ERP system with automated reorder triggers at defined reorder points.
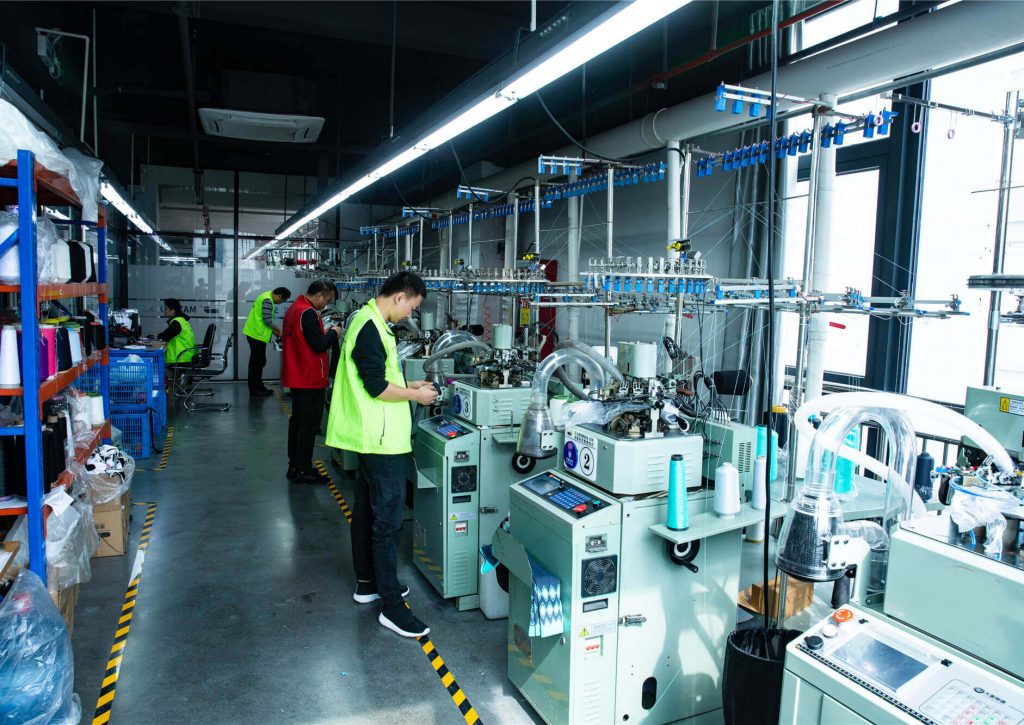
This is where it gets interesting… Partner with Jiaxing Max Hosiery Co., Ltd. our specialized sock factory founded in 2014. We hold OEKO‑TEX® Standard 100 BSCI and ISO 9001 certifications ensuring materials safety social compliance and quality control. Our MOQ starts at 500 pairs per color and style with lead times of 25–35 days. We offer two‑day sample production free DWR testing and private‑label packaging options. Our DDP shipping service delivers to your warehouse door simplifying landed‑cost calculations. Choose us as your long‑term manufacturing partner to benefit from over USD 27 million annual export capacity and responsive service from design through delivery.
Planning Element | Detail | Benefit |
---|---|---|
Forecasting | Seasonal calendar analysis | –30% stock‑outs |
Safety Stock | 50% extra buffer | Emergency order coverage |
Pricing | Tiered volume discounts | Up to 15% cost savings |
Factory Credentials | OEKO‑TEX® BSCI ISO 9001 | Quality & compliance assurance |
Conclusion
Selecting waterproof socks for retail involves understanding core technologies demand drivers and supply chain intricacies. From membrane science and DWR coatings to sewing techniques storage and DWR refresh methods each element affects performance and longevity. Customization and proactive issue management elevate brand value while data‑driven bulk planning optimizes cost and availability. Partnering with a certified factory like Jiaxing Max Hosiery Co., Ltd. ensures products meet strict quality standards and delivery timelines. Leverage these insights to source showcase and support waterproof socks that exceed customer expectations every season.
FAQ
What are waterproof socks?
Waterproof socks combine membranes DWR coatings and sealed seams to keep water out while allowing sweat vapor escape.
How does the waterproof membrane work?
Microporous membranes block liquid water yet permit vapor diffusion through submicron pores.
How do I maintain the waterproofing?
Use cold gentle washes avoid softeners and apply wash‑in or spray‑on DWR treatments every 10–15 washes.
Where can I source certified waterproof socks in bulk?
Partner with factories holding OEKO‑TEX® BSCI and ISO 9001 certifications offering MOQs from 500 pairs and DDP terms.
What customization options are available for B2B orders?
Options include Pantone‑matched colors embroidery heat transfers reflective trim and custom packaging.