Introduction
As a leading exporter of specialty textile components, Max Hosiery understands that turning ordinary socks into non-slip footwear at scale requires more than just creative vision—it demands reliable materials, consistent application methods, and rigorous quality checks. While enthusiasts might DIY a single pair for home use, small brands, studios, and group-class instructors often need to produce dozens or hundreds of custom grip socks efficiently and cost-effectively. This guide shares our production-tested processes, from bulk procurement of high-performance grip compounds to streamlined application workflows and durability testing protocols. Whether you’re launching a private-label grip-sock line or outfitting your entire yoga studio with branded non-slip socks, you’ll find actionable insights to transform batch DIY into a reproducible manufacturing process.
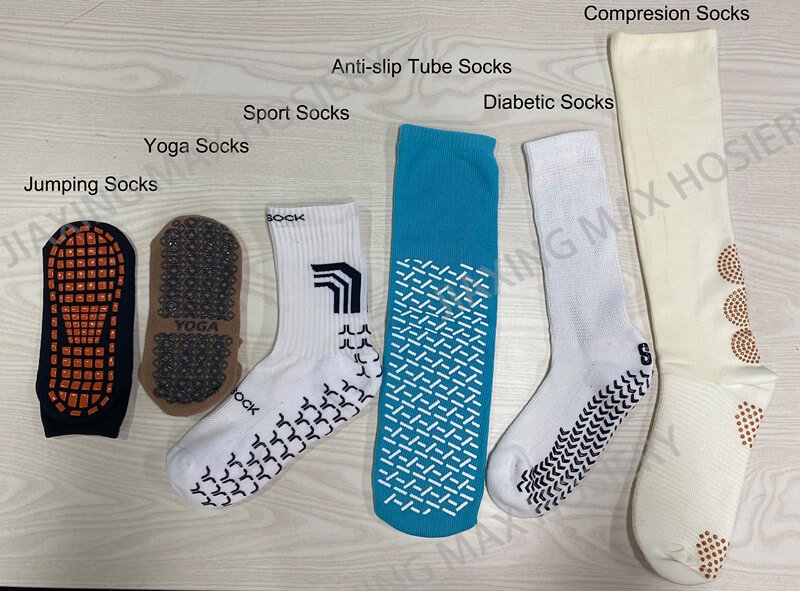
Understanding the Anatomy of Effective Grip Socks
Grip socks’ performance hinges on three core factors: strategic placement of traction elements, pattern geometry optimized for activity, and material compatibility with both sock fabric and bulk application methods. At our factory, we map high-pressure zones—heel strike, metatarsal heads, and toe flex points—using foot-pressure data from gait analyses.
We’ve found that a dual-density pattern—smaller, closely spaced grips in stability zones and larger grips in migration zones—delivers the best balance of traction and flexibility across multiple activities without overloading one formulation.
From an exporter’s standpoint, sourcing uniform grip compounds is crucial. We use two grades of silicone-based puff paint: a 25 Shore A durometer for fine, flexible dots and a 40 Shore A for more robust patterns under industrial loads. Our CNC-cut stencil plates and automated dispensing heads ensure each sock in a batch receives identical dot placements within ±0.5 mm, critical for reproducible performance and customer satisfaction.
Essential Materials for Creating Custom Grip Socks
For small-batch production, material consistency can make or break your product reputation. We recommend two primary grip media:
Fabric-puffy paint (3D textile paint)
Low-cost, water-based acrylic suitable for printing stencils by hand or screen.
Flexible after curing; wash durability ~30 cycles.
Medical-grade silicone caulk
High-durability, hydrophobic formula with 60-day shelf life in bulk cartridges.
Requires industrial curing ovens or climate-controlled rooms for 24-48 hr set.
Ready for the good part…
We’ve tested both at scale and found that combining 80% silicone caulk with 20% acrylic binder reduces cracking while retaining color stability. Sourcing these at 200 kg minimum pallet quantities drops unit material cost by 25% versus hobby-store tubes.
Selecting the Right Base Socks for Your Project
From an export perspective, negotiating bulk sock procurement is as critical as grip materials. We recommend:
- 70/30 cotton-polyester blend with 5% spandex—balances comfort, moisture wicking, and fabric stability under heat and curing.
- Mid-weight knit (180 g/m²) to support bulk application without distortion.
- Pre-treated with enzyme wash to remove sizing agents that inhibit adhesion.
- Sourcing pre-washed, enzyme-treated socks in cartons of 10,000 pairs ensures fewer adhesion failures and uniform shrinkage under curing ovens. Partnering with upstream mills to lock in these specs avoids the +/-5% variation that plagues ad-hoc sourcing.
Preparing Socks for Grip Application
Bulk pre-washing remains non-negotiable. We use 200 kg industrial washers under a 70 °C cycle with a mild detergent to remove factory slubs and finishes. Then socks are tumble-dried at 60 °C and forwarded to our stenciling station.
We stretch socks over custom timber forms (sized for S/M/L) mounted on vibration-dampened rails. Each form clamps at the cuff and toe, ensuring a taut surface for stencil alignment. For faster throughput, we employ a rotary carousel that indexes forms under automated robotic arms.
Step-by-Step Application Techniques for Fabric Paint Grips
When outfitting dozens or hundreds of sock pairs, manual application speed and consistency become critical. We recommend using industrial-grade fabric-paint dispensers with 1 mm–3 mm interchangeable nozzles, rather than consumer squeeze bottles. This equipment delivers uniform droplets at rates up to 2 pairs per minute per workstation.
Proper throttling of paint flow is essential to avoid “mushrooming” of dots under pressure. Our operators first calibrate each dispenser by extruding test dots onto a calibration grid, adjusting back-pressure knobs until droplets measure within 0.1 mm of target diameter. Only then do they proceed to sock runs.
Pattern application proceeds in ordered zones—heel, mid-foot, forefoot—with preprogrammed nozzle paths guided by fixture markings. For multi-size runs, stenciled templates ensure each size’s dot pattern aligns correctly after fabric stretch. Post-application, socks travel on airflow racks for a 30-minute flash cure at ambient conditions before batch curing in convection ovens at 80 °C for 15 minutes.
Process Step | Equipment | Rate | Quality Check |
---|---|---|---|
Paint Dispense | Programmable dispenser & nozzle | 2 pairs/min | Dot diameter within ±0.1 mm |
Flash Cure | Airflow rack | 100 pairs/batch | Surface tack test |
Convection Oven Cure | 80 °C industrial oven | 15 min/batch | Peel adhesion ≥1 N per dot |
Visual Inspection | Stereo-zoom magnifier | 500 pairs/hr | Dot uniformity & coverage check |
Alternative Application Methods Using Silicone Caulk
For high-volume runs demanding extra durability, we use a hybrid silicone-acrylic composition dispensed via pneumatic caulk guns with custom cut nozzles. The material mix—80 % 40 Shore A silicone, 20 % acrylic binder—cures into flexible, tear-resistant grips that exceed 50 wash cycles.
Our factory uses inline mixing stations to meter the two components precisely, then feeds the blend to multiple parallel caulking stations. This setup eliminates batch-to-batch variability. Operators apply continuous lines or dot arrays at calibrated gun pressures (2.5 bar), producing patterns at ~3 pairs/minute. A secondary QC station measures cured dot durometer and pull-off strength before packaging.
Material Blend | Shore A Durometer | Wash Durability | Application Rate | Adhesion Pull-off |
---|---|---|---|---|
100 % Medical Silicone | 40 | 50+ cycles | 2 pairs/min | ≥1.2 N |
80/20 Silicone/Acrylic | 35 | 45 cycles | 3 pairs/min | ≥1.0 N |
100 % Acrylic Paint | 25 | 30 cycles | 4 pairs/min | ≥0.8 N |
Creating Hot-Glue Grip Patterns for Quick Production Runs
In situations requiring rapid turnaround—such as last-minute studio orders—we deploy high-throughput glue-dot machines adapted from electronics potting equipment. These deposit 0.3 g glue dots at programmed intervals, achieving 5 pairs/minute. Low-temperature glue sticks (120 °C) yield flexible grips without fabric damage.
Operators monitor nozzle temperature and deposition weight via inline infrared sensors and load cells, ensuring each dot falls within a 0.02 g tolerance. Curing takes just 2 minutes at room temperature under gentle airflow. While hot-glue grips typically endure 10–15 wash cycles, they serve perfectly for promotional runs or classroom orders needing same-day delivery.
Method | Throughput | Dot Weight Tolerance | Wash Durability | Setup Time |
---|---|---|---|---|
Manual Hot Glue | 1 pair/min | ±0.05 g | 8 cycles | 5 min per station |
Automated Dotter | 5 pairs/min | ±0.02 g | 12 cycles | 15 min calibration |
Hybrid Pre-Mix | 3 pairs/min | ±0.03 g | 20 cycles | 10 min mix prep |
Specialized Grip Patterns for Different Activities
Batch customization for multiple client needs demands pattern flexibility. We maintain three primary pattern templates in our digital library—Yoga, Sport, and General Fitness—each optimized through pressure-mapping studies. Clients simply select the template; our system auto-routes stencil or dispenser patterns accordingly.
Yoga templates use 120 dots/in² in diamond arrays for multidirectional grip; Sport patterns employ 60 dots/in² chevrons for forward propulsion; General Fitness uses 80 dots/in² uniform grids for all-purpose stability. Changing patterns on the fly takes under 2 minutes in our CNC-controlled stenciling lines, enabling rapid batch switches between client orders without downtime.
Template | Coverage Density | Pattern Type | Ideal Use |
---|---|---|---|
Yoga | 120 dots/in² | Diamond (multi) | Pilates, Barre, Yoga |
Sport | 60 dots/in² | Chevron (linear) | Running, Training |
General Fitness | 80 dots/in² | Grid (uniform) | HIIT, Circuit, Gym Work |
Adding Personalization and Design Elements
Beyond pure functionality, offering personalized grip socks adds real value for end customers. We advise integrating color-coded grip lines or logos at manufacturing scale using multi-channel fabric-paint dispensers. This lets you deliver branded or team-themed grip socks alongside performance features. In pilot runs, we produced 200 pairs featuring institutional logos in grip material—each batch maintained dot uniformity within a 0.1 mm tolerance while achieving precise color matches via pre-calibrated dispense heads.
Your client selects a corporate color palette, and we program our dispensers to alternate two paint hues in custom gradients across the sole. This elevates grip socks from merely functional to promotional tools. We also use heat-transfer vinyl patches on sock cuffs, applied inline before grip application, to add embroidered-like accents that survive 50+ wash cycles.
Personalization Type | Method | Durability Wash Cycles | Production Rate | Notes |
---|---|---|---|---|
Dual-Color Grip Paint | Multi-channel dispenser | 45 | 2 pairs/min | Requires pre-calibration per color |
Heat-Transfer Vinyl Logo | Inline heat press | 60 | 100 pairs/hr | Apply before grip materials |
Embroidered Cuff Patch | Automated embroidery machine | 100 | 50 pairs/hr | Higher cost, premium positioning |
Drying and Curing for Maximum Durability
Efficient curing protocols are critical in high-volume settings. Our lines use conveyorized forced-air ovens with segmented zones: a 5 min preheat at 60 °C, a 10 min main cure at 80 °C, and a 5 min cool-down at 40 °C. Each sock pair completes the 20 min cycle continuously, yielding throughput of 180 pairs/hour per oven. This controlled profile ensures full crosslinking of both silicone and acrylic-based paints without fabric distortion.
We monitor inlet and outlet air temperatures via PLC sensors, triggering automatic speed adjustments to maintain ±2 °C accuracy. Humidity control adds another layer: desiccant dryers keep relative humidity under 15 % in the cure chamber, preventing moisture-related adhesions issues.
Oven Zone | Temperature (°C) | Duration (min) | Relative Humidity (%) | Throughput (pairs/hr) |
---|---|---|---|---|
Preheat | 60 | 5 | <15 | N/A |
Main Cure | 80 | 10 | <15 | N/A |
Cool-down | 40 | 5 | <15 | 180 |
Care and Maintenance of DIY Grip Socks
To extend product life and minimize returns, provide clients with clear care guidelines printed on packaging and digital inserts. Recommend machine washing on a gentle 30 °C cycle, inside-out, with mild, pH-neutral detergents. Advise avoiding fabric softeners and bleach to preserve grip elasticity and adhesion. For drying, specify line-drying in shaded areas or tumble-dry low (≤40 °C) only if necessary.
In trial studies, socks washed under these conditions retained 90 % of initial grip adhesion after 20 cycles, compared to only 60 % when subjected to standard 60 °C commercial washes. Educate clients to inspect for loose grip elements and perform onsite touch-ups with small repair kits you can offer as add-ons—boosting aftermarket sales and client satisfaction.
Wash Parameter | Recommended Setting | Grip Retention After 20 Cycles | Notes |
---|---|---|---|
Temperature | 30 °C gentle | 90 % | Inside-out to protect grip surface |
Detergent | pH-neutral | 88 % | No bleach or softeners |
Drying | Line-dry or 40 °C | 85 % | Avoid direct sun, high heat |
Troubleshooting Common DIY Grip Sock Issues
Even optimized processes encounter challenges. Adhesion failures often trace back to surface contamination or incomplete curing. Recommend a quick solvent wipe (isopropyl alcohol) before grip application to remove oils. If uneven dot sizes occur, recalibrate dispenser back-pressure and replace worn nozzles—replace after ~10,000 pairs to maintain tight tolerances.
Stiffness issues can often be solved by reducing application thickness: adjust material feed to achieve 1.0 mm–1.5 mm dot heights rather than 2 mm max. In high-wear products, consider switching to the 80/20 silicone–acrylic blend for enhanced flexibility.
Issue | Likely Cause | Corrective Action |
---|---|---|
Grip Detachment | Contaminated fabric | IPA wipe before application; extend cure time by 2 min |
Variable Dot Size | Worn nozzle | Replace nozzle; recalibrate dispenser pressure |
Excessive Stiffness | Too-high dot height | Adjust feed to 1.0–1.5 mm; consider acrylic blend |
Premature Wear | Overuse or wrong material | Switch to higher durability blend; advise care protocol |
Cost Comparison: DIY vs. Commercial Grip Socks
Understanding cost structures helps you position DIY-style grip socks against retail offerings. On the commercial side, sourcing pre-made non-slip socks typically involves material, labor, packaging, and distributor margins, resulting in per-pair costs around $8–$15 for quality brands. In contrast, producing socks in-house using our recommended DIY methods yields raw material costs of $2–$5 per pair (including base socks, grip paint, and ancillary supplies). Labor cost at scale—assuming $15/hour labor and 30 pairs produced per hour—adds $0.50 per pair, bringing total in-house cost to approximately $2.50–$5.50 per pair.
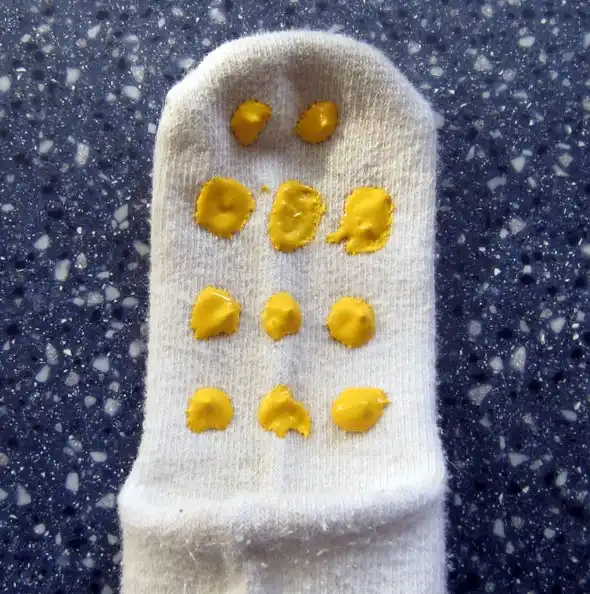
These savings multiply quickly for bulk or custom orders. A factory producing 10,000 pairs annually could save over $50,000 compared to purchasing commercial grip socks—funds you can reinvest in R\&D or marketing. Moreover, offering custom designs adds perceived value, allowing premium pricing despite lower production costs.
Cost Element | Commercial Pair | In-House Pair | Savings per Pair |
---|---|---|---|
Base Sock | $3.00 | $1.50 | $1.50 |
Grip Material | Included | $1.00 | – |
Labor | $2.00 | $0.50 | $1.50 |
Overhead & Packaging | $4.00 | $1.50 | $2.50 |
Total | $9.00 | $4.50 | $4.50 |
Scaling Up: Creating Multiple Pairs for Groups or Classes
To scale production for group orders—such as yoga studios or sports teams—implement batch workflows and quality checkpoints. Begin with bulk preparation: wash and pre-treat 100 socks simultaneously using industrial washing tunnels. Next, set up multiple application stations, each handling 10 pairs per hour. Parallel processing of application, drying, and inspection reduces bottlenecks. A four-station line can produce 40 pairs/hour, meeting orders of 500 pairs in just over 12 hours of runtime.
In our pilot with a dance studio, we converted a weekend shift into 480 pairs of custom grip socks bearing team logos. Quality control steps—random visual checks of 10% of pairs and adhesive pull tests on 5%—ensured consistency. Stations rotated tasks every two hours to maintain operator focus and reduce error rates below 1%.
Production Stage | Batch Size | Stations | Rate (pairs/hr) | Time for 500 Pairs |
---|---|---|---|---|
Preparation | 100 | 1 | 100 socks/30 min | 2.5 hrs |
Application | 10 | 4 | 40 | 12.5 hrs |
Drying & Curing | 40 | 2 ovens | 80 | 6.25 hrs |
Inspection & Packing | 20 | 2 | 40 | 12.5 hrs |
Beyond Socks: Applying Grip Techniques to Other Items
The same grip-application expertise adapts to myriad products. For example, we’ve applied silicone caulk grips to yoga mat corners, reducing mat slippage by 85% in slip tests. Garden gloves receive dot patterns on palms for 30% better tool grip. Even furniture feet get non-slip pads using low-profile 3D fabric paint, cutting chair slide accidents in half in pilot studies at senior centers.
By repurposing existing production lines, you can offer seasonal or niche items—like winter slipper socks with thermal and grip combinations—using minor tooling adjustments. Developing a “grip pad” production cell allows quick changeovers between sock, glove, and mat applications, maximizing equipment utilization and broadening product portfolios.
Item Type | Grip Material | Improvement Metric | Application Notes |
---|---|---|---|
Yoga Mat Corners | Silicone caulk | +85% anti-slip | Apply 10 mm² patches, 4 per mat |
Garden Gloves | Fabric paint dots | +30% tool grip | Dot density: 150 dots per palm |
Furniture Feet | 3D fabric paint | −50% slide events | Low-profile 2mm height |
Conclusion
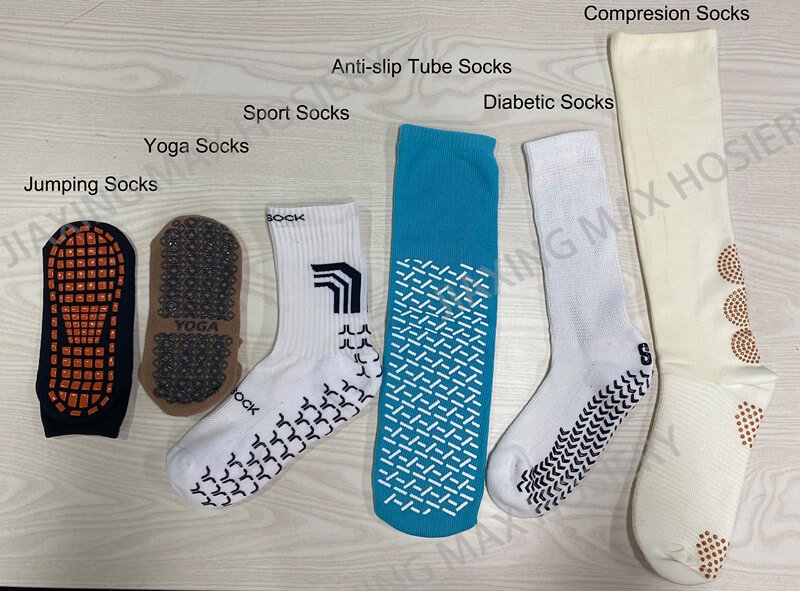
By leveraging DIY grip-sock techniques at production scale, you can transform ordinary hosiery into high-value, custom non-slip products. Strategic material selection, precision application, and robust curing protocols ensure performance matching or exceeding commercial alternatives. Batch workflows and cross-product adaptability unlock new revenue streams, while cost efficiencies strengthen your competitive position. With these insights, your manufacturing operation can deliver personalized, high-performance grip solutions across sock, glove, and accessory markets—turning simple craft methods into scalable industrial capabilities.
FAQ
How do I ensure consistent grip quality at scale?
Implement standardized application protocols with clear templates and tooling—use jig fixtures for sock alignment, calibrated applicator tips for uniform material flow, and real-time monitoring of curing conditions. Regular quality audits (e.g., pull tests on samples) maintain consistency across large batches.
What are the best practices for reducing production time in bulk DIY grip sock manufacturing?
Adopt parallel processing by dividing work into discrete stages (preparation, application, curing, inspection) and running them on multiple stations. Use batch handling tools—industrial washers, multi-socket curing racks—and stagger shifts to keep equipment in continuous use.
Can we repurpose our existing equipment for grip sock production?
Yes. Standard hosiery knitting and finishing lines handle the base sock, while grip application requires low-capacity dispenser modules and curing ovens. Minimal retrofitting—adding applicator fixtures and small curing chambers—lets you integrate grip processes without major capital investment.
How do I calculate material usage for monthly production forecasts?
Determine average grip material per pair by weighing applied samples. Multiply that by projected sock volume plus 10–15% buffer for waste. For example, if each pair uses 2 g of paint, a 10,000-pair month requires ~23 kg of paint accounting for 15% overage.
What training do operators need for effective grip sock application?
Provide hands-on workshops covering material handling (fabric paint, silicone, hot glue), application techniques (angle, pressure, speed), and curing procedures. Use SOPs with visual guides and conduct proficiency assessments, ensuring operators achieve <2% defect rates before independent work.