In recent years, grip socks have evolved from specialized athletic equipment to mainstream accessories used across diverse applications—from yoga studios and hospital corridors to toddler playrooms and elderly care facilities. This widespread adoption stems from their unique functionality: providing secure footing on smooth surfaces where conventional socks might slip. While consumers readily appreciate the benefits these specialized socks provide, few understand the sophisticated manufacturing processes and material science that transform ordinary textiles into effective grip-enhanced footwear. This comprehensive exploration takes you behind the scenes of grip sock production, revealing the engineering considerations, material selections, and manufacturing techniques that create these increasingly essential accessories.
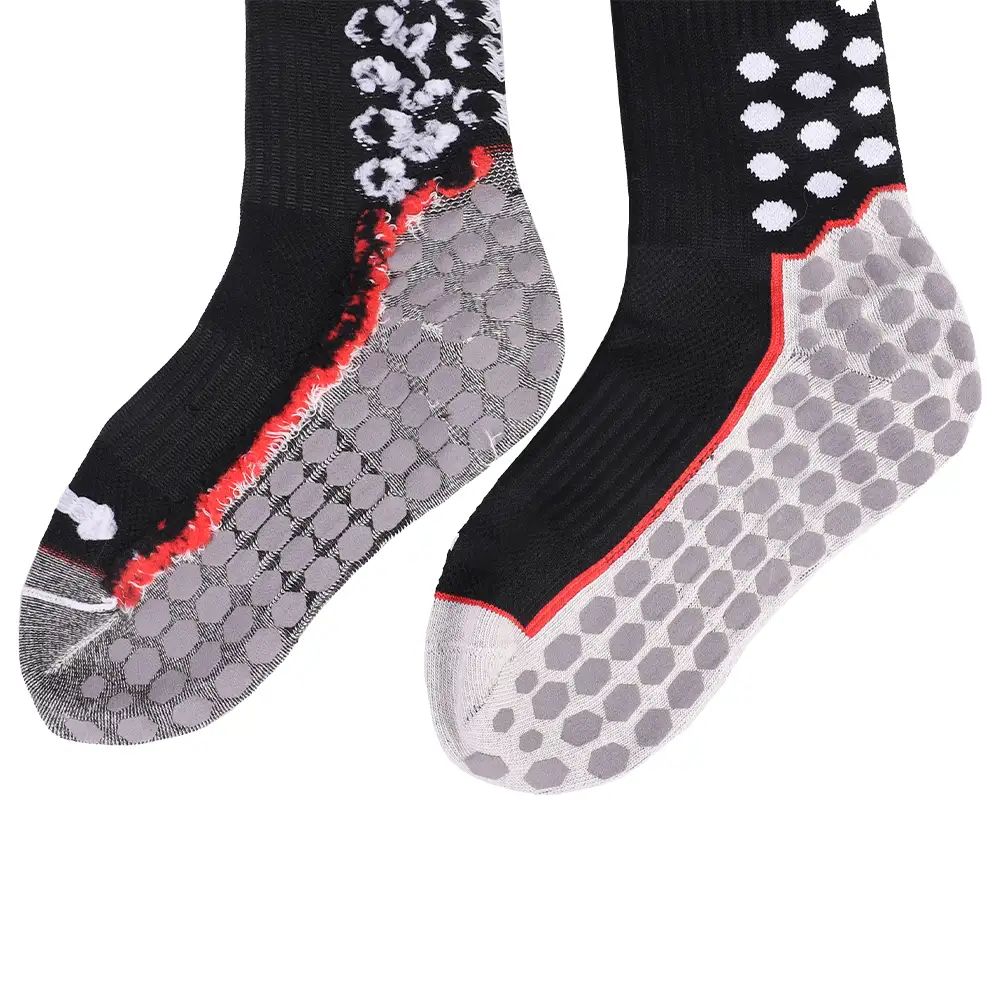
The Evolution of Grip Technology: A Brief History
The concept of enhancing footwear with non-slip properties dates back centuries, with various cultures developing solutions for specific environmental challenges. Traditional Japanese tabi socks, featuring separated toes and reinforced soles, represent early attempts to improve grip while maintaining foot flexibility. However, modern grip sock technology emerged more recently, evolving primarily through innovations in the athletic and medical sectors. The 1990s saw the first widespread commercial applications, with yoga practitioners adopting early versions to maintain stability during challenging poses on smooth studio floors. These initial designs featured rudimentary rubber dots applied to conventional athletic socks, providing basic friction enhancement but often lacking durability through repeated washing. The medical field simultaneously developed non-slip hospital socks to prevent patient falls, focusing on functionality rather than comfort or aesthetics. These parallel development paths eventually converged as manufacturers recognized the broader applications for grip-enhanced footwear across different user groups. The early 2000s brought significant advancements in both materials and application techniques, with silicone emerging as the preferred grip medium due to its durability, flexibility, and heat resistance. Manufacturing processes evolved from manual application to automated systems capable of creating precise, consistent grip patterns at scale. The most recent decade has seen further refinement in both performance and aesthetics, with specialized designs emerging for specific activities ranging from barre classes to trampoline parks. This evolution continues today, with ongoing innovations in eco-friendly materials, manufacturing efficiency, and application-specific grip patterns that optimize performance for particular uses while maintaining comfort and durability.
Base Materials: Selecting the Perfect Fabric Foundation
For athletic grip socks, synthetics like polyester, nylon, and polypropylene are popular due to their moisture management, shape retention, and quick-drying properties. These materials help maintain grip placement and reduce soggy sock issues during high-intensity activities. Ready for the good part? they also provide enhanced odor resistance, crucial for studio or active wear environments.
Specialty materials, like bamboo-derived rayon, offer natural antimicrobial benefits for sensitive skin, while merino wool ensures temperature regulation and moisture management for outdoor applications. Compression-focused grip socks use high-elastane fabrics to deliver graduated pressure without compromising grip functionality.
Knitting construction also impacts performance. Circular knitting ensures seamless comfort, while fully-fashioned knitting provides anatomical shaping for a better fit and grip placement. The knit density affects durability and grip support—tighter knits offer more grip but may reduce flexibility and comfort.
The Anatomy of a Grip Sock: Key Components
The fabric used in grip socks plays a crucial role in both performance and user comfort. But here’s the kicker… unlike regular socks, grip socks need to balance comfort with durability to maintain grip during repeated use and washes. Cotton blends offer comfort and breathability but may stretch over time, reducing grip effectiveness.
For athletic grip socks, synthetic materials like polyester, nylon, and polypropylene are favored for their moisture-wicking, shape-retention, and quick-drying properties. Ready for the good part? these materials not only help maintain grip placement but also offer enhanced odor resistance—essential for active environments.
Specialty fabrics like bamboo-derived rayon provide natural antimicrobial properties, making them ideal for sensitive skin, while merino wool offers temperature regulation for outdoor use. Compression-style grip socks use high-elastane fabrics to deliver graduated pressure without compromising grip functionality.
The knitting technique also impacts performance. Circular knitting provides seamless comfort, while fully-fashioned knitting offers anatomical shaping for a better fit. Tighter knit densities improve grip but may reduce flexibility and comfort.
Material | Key Feature | Benefit |
---|---|---|
Cotton Blends | Comfort, breathability | Ideal for everyday wear but less durable |
Polyester/Nylon | Moisture-wicking, durable | Maintains shape and grip positioning |
Bamboo Rayon | Antimicrobial, soft | Perfect for sensitive skin |
Merino Wool | Temperature regulation, moisture control | Great for outdoor activities |
High-Elastane (Compression) | Graduated pressure, flexibility | Supports circulation and grip placement |
Grip Pattern Design: Engineering the Perfect Friction Surface
The arrangement of grip elements on the sock sole plays a key role in its functionality and user experience. But here’s the kicker… the design must balance friction for stability, flexibility for movement, and pressure distribution while adhering to manufacturing limitations.
The process begins by analyzing the specific activity to determine where grip is needed most. For example, grip patterns for yoga socks differ from those used in hospital settings or for toddlers learning to walk. Full-coverage designs offer consistent stability but can reduce flexibility and breathability while increasing costs. Alternatively, partial coverage focuses grip on high-contact areas, such as the ball of the foot and heel, allowing for better movement control in activities that require specific transitions.
The shape and density of grip elements also affect functionality. Circular dots are common for multidirectional grip and are easier to manufacture. More complex patterns, like linear ridges or hexagons, provide enhanced grip in specific directions but can be more challenging and costly to produce. The spacing between grip elements affects comfort, with denser patterns offering more stability but potentially limiting flexibility.
Modern design tools now help engineers simulate various configurations and optimize grip patterns. This is where it gets interesting… digital tools enable faster, cost-effective refinement of designs, creating more effective, application-specific solutions.
Silicone Application Techniques: Creating Grip Elements
The application of grip materials to socks is one of the most technically complex aspects of manufacturing, directly affecting performance and durability. But here’s the kicker… various methods offer distinct advantages depending on the design and material requirements. The most common technique is screen printing, which uses specialized screens to apply a silicone or PVC compound onto the sock in a precise pattern. The material then undergoes curing to solidify the grip elements. This method is cost-effective and provides good precision, though the resulting grip elements may wear more quickly than other methods.
Injection molding offers a more pronounced grip design by molding the material into specific shapes, creating more durable and effective grip features. However, it requires more specialized equipment and leads to slower production speeds, increasing costs. Heat transfer processes are also widely used, where pre-formed grip patterns are applied to socks using heat and pressure, ensuring consistency in production. Lastly, dipping methods, though less common, involve immersing parts of the sock in liquid grip compounds, providing seamless coverage but less precision for intricate patterns.
Application Method | Advantages | Disadvantages |
---|---|---|
Screen Printing | Cost-effective, precise for patterns | Thin grip elements, wear quickly |
Injection Molding | Durable, enhanced grip elements | Expensive equipment, slower speed |
Heat Transfer | Consistent results, easy application | Limited for complex patterns |
Dipping | Seamless coverage | Less precision, simple designs only |
Beyond Silicone: Alternative Grip Materials
While silicone remains the dominant grip material, other options are emerging to meet different performance and sustainability needs. Ready for the good part? PVC compounds are commonly used as a cost-effective alternative to silicone, offering good durability and grip. However, environmental concerns about PVC’s production and disposal have prompted the search for more sustainable materials.
Natural rubber derivatives, such as latex, provide renewable options with excellent grip and flexibility, though they have limitations due to allergy concerns in some users. Thermoplastic elastomers (TPEs) offer a balanced performance with the added benefit of better sustainability, combining rubber and polymer characteristics. These materials are easier to process and provide excellent elasticity for grip socks. Emerging bio-based polymers, derived from renewable resources like corn or algae, are gaining attention as sustainable alternatives, though they still face higher costs and processing challenges.
Water-based formulations offer another sustainable option, reducing harmful emissions during manufacturing. This is where it gets interesting… these compounds have evolved significantly, improving their performance and making them a viable alternative for eco-conscious manufacturers.
Alternative Material | Benefits | Challenges |
---|---|---|
PVC | Durable, cost-effective | Environmental impact, disposal issues |
Natural Rubber | Renewable, excellent grip | Allergens, limited use cases |
TPE | Versatile, easier to process | Limited availability, costlier |
Bio-based Polymers | Sustainable, renewable resources | Higher costs, complex processing |
Water-based Formulations | Eco-friendly, reduced VOC emissions | Initial performance limitations |
Quality Control in Grip Sock Manufacturing
Grip socks are specialized products that require strict quality control to ensure their performance and durability. But here’s the kicker… these socks need more than just basic fabric checks; they require detailed testing to guarantee grip, comfort, and functionality. The first major quality check is grip effectiveness, measured through friction testing on surfaces like hardwood and tile. This verifies that the sock provides the right level of stability for its intended use, whether for medical safety or athletic performance.
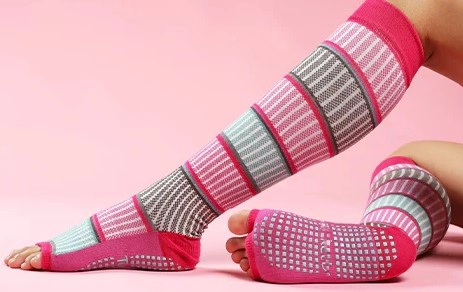
The durability of grip elements is tested with wash resistance protocols, which assess how well grip performance holds up after multiple washes. High-quality grip socks must maintain their grip performance even after several laundering cycles. Ready for the real story? standardized tests measure peel strength to ensure that grip elements stay securely attached to the fabric, preventing peeling or degradation over time. Additionally, dimensional stability checks make sure the socks retain their size and shape, providing consistent comfort and fit.
Material safety testing is crucial, particularly when grip socks are used by vulnerable populations like children, the elderly, or medical patients. These tests ensure compliance with safety regulations, checking for harmful chemicals or substances that could cause irritation or injury. This is where it gets interesting… manufacturers must invest in advanced testing technologies to ensure that their products meet all safety standards, ensuring long-lasting consumer trust.
Testing Focus | Key Process | Outcome |
---|---|---|
Grip Effectiveness | Friction coefficient tests | Confirms stability for intended use |
Wash Resistance | Multiple wash cycles | Ensures durability over time |
Structural Integrity | Peel strength, abrasion resistance | Prevents grip element detachment |
Material Safety | Restricted substance testing | Ensures no harmful chemicals |
Specialized Manufacturing for Different Applications
Grip socks are not one-size-fits-all; they need to be tailored for specific activities and user groups. But here’s the kicker… the manufacturing process adapts to the needs of different users—whether athletes, children, elderly individuals, or medical patients. Athletic grip socks designed for activities like yoga or Pilates focus on targeted grip placement that supports specific movements and positions. These socks are designed to be flexible while maintaining enough friction to prevent slipping during dynamic poses.
Hospital grip socks are built for safety above all else. These socks use full-coverage grip patterns, providing stability regardless of foot position, and are made with materials that are comfortable for sensitive skin and easy to wear for those with limited dexterity. Ready for the good part? these socks are designed to be durable enough for frequent high-temperature washing, which is common in medical environments.
For children, especially early walkers, grip socks are manufactured to ensure safety while supporting natural foot movement. Soft materials and seamless designs help prevent irritation, while grip elements are applied carefully to avoid restricting growth. This is where it gets interesting… these socks ensure safety without compromising foot development, offering a crucial balance between protection and comfort.
Elderly care applications have their own set of requirements. These socks are designed with extra stretch openings for easier wear, along with padding in high-pressure areas for added comfort. Grip patterns ensure stability during transitions, such as getting out of bed or moving from sitting to standing. But here’s the kicker… material selection emphasizes warmth for often cold extremities while allowing for breathability to manage moisture.
Application | Key Features | Manufacturing Focus |
---|---|---|
Athletic Grip Socks | Targeted grip zones, flexibility | Performance and movement support |
Hospital Grip Socks | Full-coverage grip, easy donning | Fall prevention, durability for medical use |
Children’s Grip Socks | Soft, seamless, supportive grip | Foot development and comfort |
Elderly Grip Socks | Extra stretch, padding in high-pressure areas | Mobility support, warmth and breathability |
The Role of Technology in Modern Grip Sock Production
Technological advancements have revolutionized grip sock production, shifting from manual processes to sophisticated, automated systems that improve consistency and performance. But here’s the kicker… innovations like computer-aided design (CAD) systems have redefined grip pattern development, allowing for precise customization based on biomechanical data. This enables more functional and effective grip placements by simulating different configurations digitally before prototyping, reducing material waste and speeding up the development process.
Automated knitting technology has streamlined the creation of sock bodies, allowing machines to produce anatomically shaped socks with complex structures like targeted compression zones and ventilation panels. Ready for the good part? these systems ensure consistent reproduction of designs across production runs, with minimal variation, even when switching between sizes and designs. Robotic grip application systems have replaced manual methods, enhancing precision in grip material placement. Computer-controlled systems ensure accuracy, while automated vision systems verify proper sock positioning. The result? More complex, detailed grip patterns that improve both function and design flexibility.
Digital quality control tools further enhance sock consistency. Automated friction testing measures grip effectiveness, and wash testing simulates real-world durability, ensuring products meet performance expectations. Manufacturing execution systems (MES) integrate all these technologies into one cohesive workflow, streamlining scheduling, material tracking, and quality control. This is where it gets interesting… the data captured through these systems enables real-time adjustments, optimizing production and reducing defects.
Technological Element | Function | Benefit |
---|---|---|
Computer-Aided Design (CAD) | Precision grip pattern design | Faster development, reduced material waste |
Automated Knitting Machines | Complex anatomical designs and structures | Consistent product quality, rapid scalability |
Robotic Grip Application | Automated, precise grip material placement | Detailed, reliable grip patterns |
Digital Quality Control | Friction and wash testing, dimensional verification | Ensures durability and consistent performance |
Sustainability Challenges and Innovations in Grip Sock Production
Sustainability is becoming an essential focus for grip sock manufacturers. But here’s the kicker… many of the materials traditionally used for grip socks, like silicone and PVC, have significant environmental impacts due to their petroleum origins. To address this, forward-thinking manufacturers are exploring bio-based alternatives, including materials derived from plant oils and agricultural byproducts. These innovative materials maintain performance while reducing reliance on fossil resources and lowering carbon footprints.
Textile sustainability also plays a vital role. Conventional cotton uses large amounts of water and pesticides, while synthetic fibers are often petroleum-based. Ready for the good part? manufacturers are increasingly turning to organic cotton, recycled polyester, and sustainable fibers like bamboo or eucalyptus. These alternatives offer lower environmental impacts while often improving performance, such as better moisture management and natural antimicrobial properties.
Manufacturing efficiency drives further sustainability. This is where it gets interesting… advances like solution dyeing significantly cut water use by adding color during fiber formation, reducing the need for water-intensive post-production processes. Automated systems also minimize waste by optimizing fabric use and reducing material waste in grip application. Energy-efficient curing methods, such as LED or infrared systems, further reduce environmental impact compared to traditional methods.
Packaging sustainability is another area of focus, with manufacturers reducing packaging material through minimalist designs and using recyclable or recycled materials. But here’s the kicker… some companies now offer take-back programs to recycle worn grip socks, closing the loop on product life cycles and reusing materials for new products. These efforts not only reduce waste but also align with consumer demand for environmentally responsible practices.
Sustainability Focus | Innovation | Benefit |
---|---|---|
Bio-Based Grip Materials | Plant-based alternatives to silicone and PVC | Reduced fossil resource consumption |
Sustainable Textiles | Organic cotton, recycled polyester, bamboo | Lower environmental impact, enhanced performance |
Manufacturing Efficiency | Solution dyeing, automated cutting, energy-efficient curing | Reduced water use, less material waste |
Packaging Sustainability | Minimalist designs, recyclable materials | Reduced waste, eco-friendly practices |
From Factory to Feet: The Distribution and Quality Assurance Process
The journey from production to consumer use involves multiple stages to ensure grip socks reach customers in perfect condition. But here’s the kicker… quality assurance is crucial in this process. Final inspection evaluates both aesthetic and functional characteristics, ensuring products meet specifications. Visual checks identify cosmetic defects like color variations or construction flaws, while physical tests verify performance features such as grip effectiveness and dimensional accuracy.
Packaging serves dual roles: protecting products during transport and providing branding for marketing. Primary packaging protects against dust and moisture, with increasing emphasis on sustainability through recycled or biodegradable materials. Retail packaging incorporates branding and essential consumer information, balancing protection with presentation.
Inventory management systems and climate-controlled warehousing maintain product quality during storage and distribution. Transportation logistics focus on cost-efficiency while safeguarding the product, with protective packaging designed for bulk shipments and direct-to-consumer fulfillment. International distribution presents additional challenges, requiring compliance with varying customs regulations and extended transit times.
Post-distribution quality assurance involves ongoing market surveillance and customer feedback. Random sampling from retail inventories and warranty programs help ensure products meet standards even after distribution. Progressive manufacturers use this data to refine production processes, ensuring consistent quality. These efforts explain the price difference between premium and budget options.
Stage | Function/Objective | Outcome |
---|---|---|
Final Inspection | Aesthetic and functional checks | Ensures product meets specs |
Packaging | Protects, brands, informs | Ready for retail and consumer use |
Inventory Management | Proper storage and handling | Maintains quality and prevents damage |
Post-Distribution QA | Customer feedback and random sampling | Refines product and manufacturing |
Conclusion
The path from basic textile to functional grip sock is a process of sophisticated engineering, material science, and meticulous manufacturing. Ready for the good part? quality grip socks stand out because of their careful material selection and technical performance. Understanding these production stages helps consumers recognize the value of well-designed grip socks, which offer a significant price premium over basic hosiery.
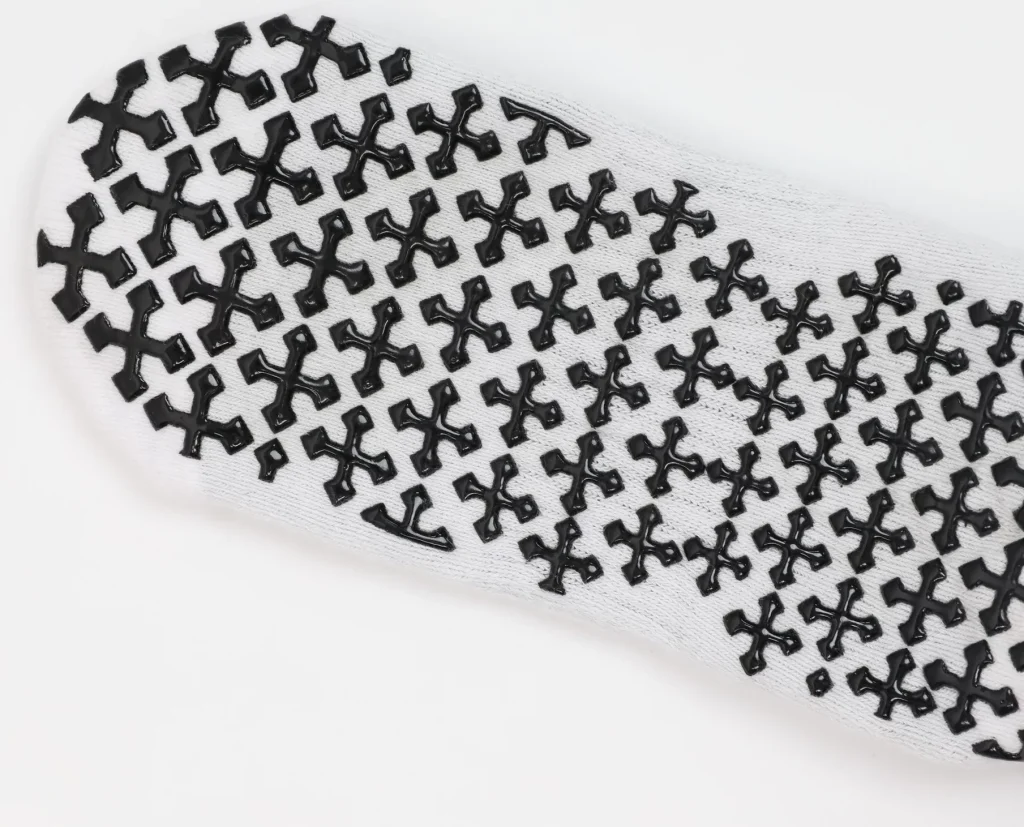
Manufacturing grip socks involves balancing comfort with structural integrity to ensure performance. The grip compounds and application techniques are what truly differentiate premium products from imitations. Quality control checks, from material selection to final testing, ensure the socks perform reliably over time.
As the demand for grip socks expands into broader markets, manufacturing technologies evolve to improve both performance and sustainability. Innovations in materials, production techniques, and quality verification will continue to shape these specialized products. With so many options on the market, understanding the manufacturing processes behind quality grip socks will guide consumers to make informed choices that meet their specific needs—whether for fitness, medical, or everyday activities.
FAQ Section
What makes grip socks different from regular socks with rubber prints on the bottom?
Professional grip socks utilize specialized materials and manufacturing processes that create durable, effective grip elements. The silicone or rubber compounds undergo specific curing processes that bond securely to the fabric base, while the patterns are engineered for optimal friction across different surfaces and movements.
How long should quality grip socks maintain their grip effectiveness?
With proper care, premium grip socks typically maintain effective grip through 30-50 wash cycles. The actual lifespan varies based on usage intensity, washing methods, and specific construction quality. Higher-quality options generally utilize more durable grip compounds and stronger bonding methods that extend functional lifespan.
Are grip socks machine washable, or will washing damage the grip elements?
Quality grip socks are designed for machine washing, though specific care enhances longevity. Turn them inside-out, use cold water and mild detergent without fabric softener, and air dry or use low heat settings. These practices prevent premature deterioration of grip elements and adhesive bonds.
Why do grip socks cost more than regular socks?
The price difference reflects specialized materials, complex manufacturing processes, and extensive quality testing. The grip compounds, application equipment, and curing systems represent significant investments, while the precision required for effective grip patterns necessitates sophisticated production technologies and rigorous quality control.
Are there environmentally friendly grip sock options available?
Yes, eco-conscious manufacturers now offer options with recycled fabric content, organic cotton, or bamboo-derived fibers. Some utilize bio-based grip compounds derived from renewable resources rather than petroleum. Look for specific sustainability certifications or transparent environmental claims from reputable brands.