Introduction: The Strategic Value of Performance Work Boot Socks in Industrial Settings
In today’s industrial procurement environment, focus has shifted toward improving worker comfort, safety, and efficiency, extending beyond standard PPE. Performance work boot socks offer a high-impact yet often overlooked opportunity. With features like targeted cushioning, moisture control, and enhanced durability, these socks support long shifts, reduce foot fatigue, and extend boot life. For procurement teams and safety managers, choosing the right socks can lower injury risk, improve worker satisfaction, and reduce turnover-related costs. This guide explores key considerations in selecting, sourcing, and implementing performance work boot socks, covering material specs, supplier evaluation, and logistics planning. Whether you’re overseeing multiple facilities or sourcing for demanding work environments, understanding this product category enables better cost control and improved operational outcomes.
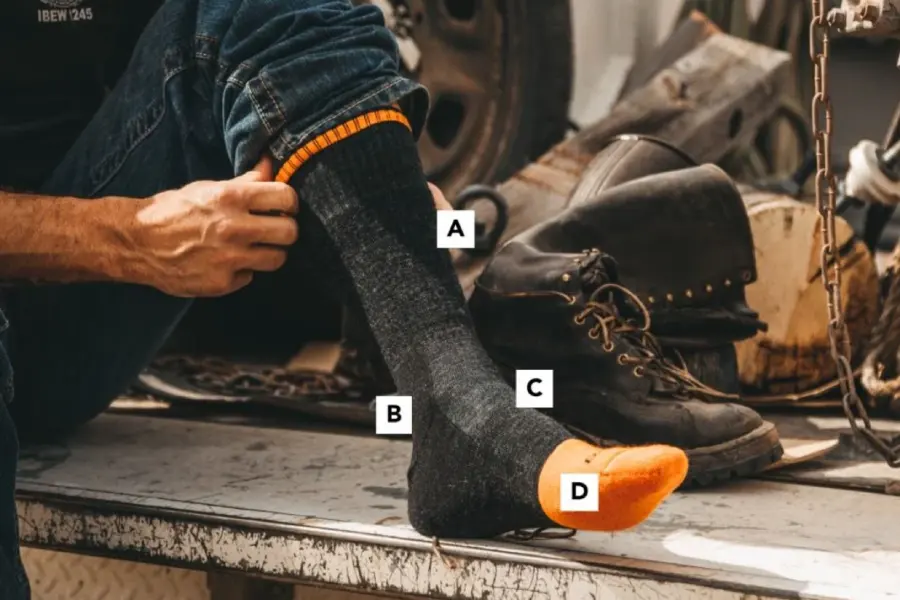
Market Analysis: Understanding the Work Boot Sock Landscape
Market Analysis: The Evolving Work Boot Sock Sector
Before choosing suppliers, procurement professionals need to understand how the work boot sock market works today—from who supplies what, to how performance features vary by job site needs.
Supplier Categories: Who Makes What
The market includes four main types of suppliers:
- Workwear Brands – Offer premium socks as part of broader apparel programs. They charge more (15–25% higher) but provide better documentation, support, and product knowledge.
- Performance Sock Specialists – Focus solely on technical socks. Their material expertise is strong, but industrial application experience can vary.
- Mass Apparel Manufacturers – Offer lower prices due to large-scale production. However, their socks may lack advanced features for demanding work settings.
- Private Label Suppliers – Let distributors or companies create custom-branded socks at 10–20% cost savings. Quality varies, so clear specifications are key.
Many buyers now combine suppliers: premium lines for critical roles, budget socks for general use. The competitive market also gives large-volume buyers room to negotiate better deals.
Performance Types: Matching Sock Features to Job Demands
Modern work boot socks aren’t generic. Key performance types include:
- Thermal Control (30–35%) – Keep feet warm or cool in extreme temperatures. Ideal for outdoor or warehouse workers.
- Cushioning Zones (25–30%) – Add comfort and impact relief for long shifts on concrete.
- Moisture Management (in 50–60% of products) – Reduce sweat, odor, and blister risk through wicking fibers.
- Durability Enhancements – Reinforced toes, heels, and soles resist wear, cutting replacement frequency.
Choosing the right mix depends on the work environment. A good sourcing strategy involves reviewing climate, shift length, and movement intensity. This ensures each department gets socks that match their job—improving comfort, safety, and cost-efficiency.
Performance Assessment: Establishing Evaluation Frameworks
A structured performance evaluation helps procurement teams select work boot socks that meet functional demands while minimizing long-term replacement costs. An effective framework covers two key areas: material construction and field performance.
Material Composition and Construction
Sock performance starts with fiber selection. High-quality work socks often blend several materials for balanced function:
- Merino wool – for warmth and odor control
- Nylon or polyamide – for durability and abrasion resistance
- Polyester – for moisture-wicking and drying speed
- Acrylic – as a cost-effective insulator
- Spandex/elastane – for fit and stretch recovery
Material density matters too. Heavier options (200+ gsm) offer more cushion but may reduce breathability. For general-purpose industrial use, 150–200 gsm socks often balance comfort and ventilation well.
Design details also impact longevity and comfort. Reinforced toes and heels, targeted cushioning, ventilation zones, and arch support bands improve fit and reduce fatigue. Procurement teams should request technical specs and consider third-party test results where available, especially if internal textile expertise is limited.
Real-World Field Testing
Lab specs alone don’t guarantee performance. Field testing captures real feedback from workers across different tasks, shifts, and boot types. Important data includes:
- Comfort scores (start-of-shift and end-of-shift)
- Moisture control (dryness after long wear)
- Durability (wear-and-wash cycles)
- Fit and boot compatibility
Ideally, trials should run for 4–8 weeks with structured evaluations and comparison against current or competitor products. Using forms and photos helps standardize responses and spot quality issues early. When environments vary, segmented testing ensures performance across job roles, climates, or foot types.
By combining construction analysis with structured field data, procurement professionals reduce guesswork and select socks that truly support workforce performance and reduce replacement frequency over time.
Procurement Strategies: Optimizing Value and Performance
Effective procurement strategies help industrial buyers get more than just a low unit price. For work boot socks, this means selecting products that meet worker needs, stay in stock reliably, and deliver strong value over time.
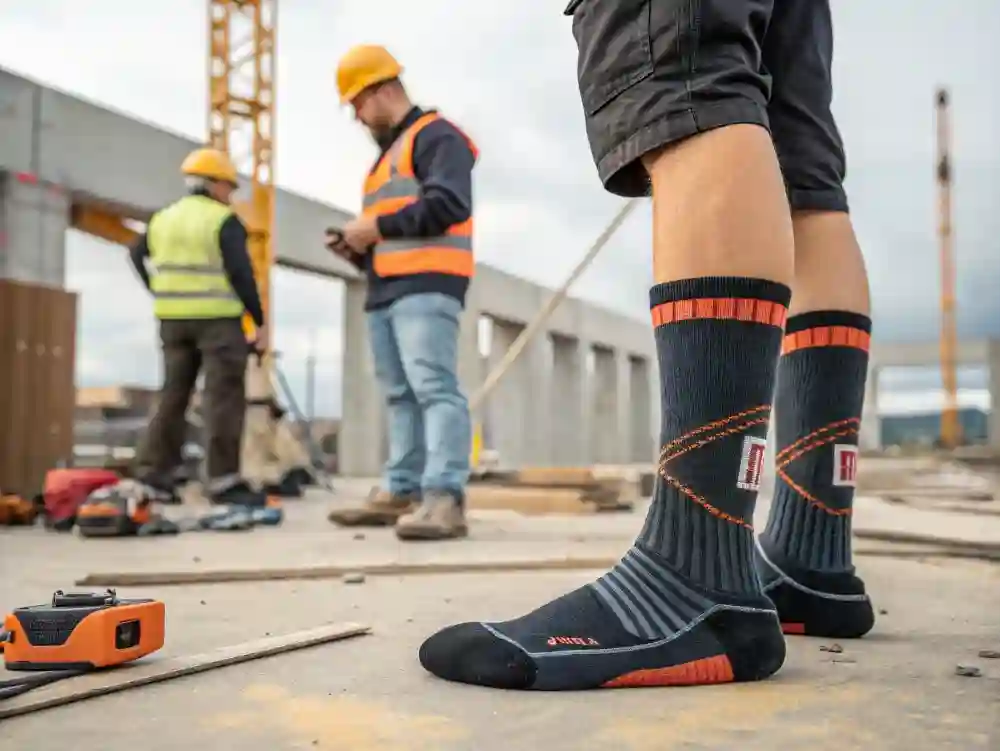
Standardization and Use Case Mapping
Standardizing work boot socks can reduce cost and simplify supply chains. Organizations that consolidate styles often see 10–20% savings from volume pricing and 15–30% lower inventory holding costs. But successful standardization depends on knowing your use cases.
Application mapping is key. Procurement teams should assess environmental conditions, movement types, and foot protection needs across departments. This helps identify where one standard sock will work—and where a specialized option is necessary. A two-tier system often works best: one core style for general use, and a few approved variants for high-heat, cold-weather, or high-friction environments.
Worker feedback during testing is essential. Engagement improves compliance and helps avoid complaints later. Communication plans should highlight comfort gains, durability, and ease of stocking. For multi-site operations, standardization enables centralized buying, easier training, and shared quality benchmarks.
Total Cost of Ownership (TCO) Focus
Buying based on price alone can miss hidden costs. Total cost of ownership (TCO) analysis reveals the full impact of sock selection. This includes not only purchase price, but also replacement frequency, admin and storage costs, and effects on worker performance.
Durable socks may cost more upfront but last two to three times longer than basic models. That reduces reordering frequency and lowers the actual cost per use. Better socks can also reduce foot fatigue, limit minor injuries, and even extend boot life by preventing interior wear from moisture or friction.
Many companies run pilot programs with different sock types, tracking comfort, lifespan, and related costs. These real-world tests support smarter long-term procurement decisions. When aligned with business goals, TCO frameworks help procurement teams move from short-term cost-cutting to long-term value generation.
Supplier Evaluation: Developing Selection Frameworks
Choosing the right supplier for work boot socks is more than comparing prices—it’s about long-term performance and support. A strong evaluation framework helps industrial buyers select partners who deliver both product quality and service reliability.
Proving Product Performance
For work boot socks, comfort and durability affect worker output. Reliable suppliers should offer third-party lab reports, case studies, or field test data to support performance claims. Internal test results can be considered, but unsupported marketing claims should carry little weight. Testing should match real work environments—like high-heat zones or chemical areas—not just lab conditions. Some buyers go further by running small-scale performance checks before full orders. Suppliers who invest in ongoing testing and collaborate with safety experts often offer better value as needs evolve.
Operational Reliability Matters
Supply chain strength is just as important. Look for suppliers with high fill rates (98%+), quick lead times (1–3 weeks), and options like consignment or blanket orders. Good customer service means fast responses, dedicated reps, and clear escalation paths. For larger programs, suppliers that offer rollout kits, training tools, or product switching support can ease transitions. Digital integration—like EDI, real-time stock visibility, or custom reports—makes ongoing ordering and tracking easier. Some even provide vending-machine-ready packs or size kits for individual workers. For global buyers, consistent product availability across regions and multi-language support also matter. Choosing suppliers who offer strong products and reliable support helps reduce risk and improve program success.
Implementation Planning: Ensuring Program Success
A smooth rollout is critical for transitioning to new work boot sock standards across industrial teams. A well-planned implementation not only minimizes disruption but also promotes long-term program success.
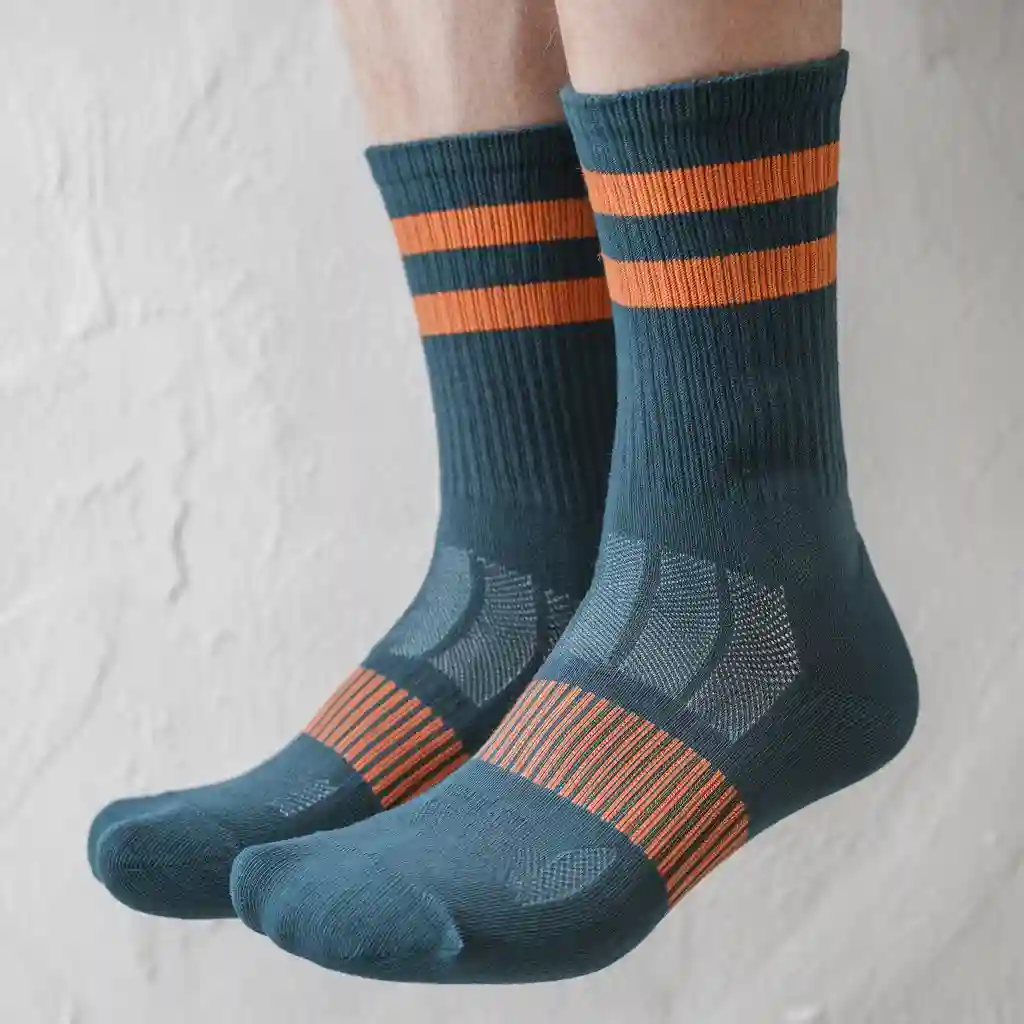
Rollout Strategy and Communication
Start with a phased rollout—testing the program in a single site or department before full deployment helps identify fit issues or process gaps. Plan rollouts during lower operational activity to reduce disruption risks.
Clear internal communication is essential. Tailor messages for different audiences:
- Managers need to understand cost-efficiency and safety outcomes.
- Supervisors should know distribution and exchange procedures.
- Workers want clarity on comfort, care instructions, and usage benefits.
Use simple materials like posters, briefings, and sizing charts. For unionized environments, early dialogue with representatives helps secure buy-in. “Product champions” within teams can assist rollout by encouraging peers and providing on-the-ground support.
Training and Monitoring
Training ensures proper use and long-term value. Short sessions, hands-on demos, and short videos are effective. Focus on:
- Proper fit and usage
- Product care to maintain grip and durability
- When to request replacements
Monitoring is just as important. Observe usage during regular safety checks or PPE audits. Collect worker feedback to refine product choice and distribution. For companies using multiple sock types, provide training on selecting the right sock for the task—this prevents misuse and protects performance. Recognizing high-compliance teams can help drive positive habits and reduce enforcement pressure. With a clear plan for communication, training, and monitoring, organizations can ensure that work boot sock programs are adopted successfully and deliver the operational results they were designed to provide.
Inventory Management: Optimizing Availability and Efficiency
Efficient inventory management is key to ensuring work boot socks are always available when needed—without overstocking or tying up excess capital. A structured approach to size planning, stocking levels, and distribution methods reduces waste, improves compliance, and supports workforce satisfaction.
Size Planning and Stock Distribution
Start with real data. Direct foot measurements are more accurate than self-reports and help avoid misallocation. If unavailable, use standard bell-curve estimates:
- Small (S): 10–15%
- Medium (M): 25–30%
- Large (L): 30–35%
- XL: 20–25%
- XXL: 5–10%
Focus stocking around high-demand sizes with 4–6 weeks of safety stock. Keep lean reserves (2–3 weeks) for extreme sizes to avoid dead inventory. Color-coded or clearly marked sizing improves issue accuracy. Some enterprises assign socks directly to employees, increasing accountability and reducing waste by up to 25%.
Distribution Models and Tracking
Inventory placement affects both access and control. Centralized storerooms simplify reordering and enable usage tracking but may limit worker convenience. Decentralized systems at department level offer faster access but increase the risk of overconsumption and stock imbalances.
Automated dispensers are gaining traction. Though costly upfront, they offer real-time usage data, automatic replenishment, and tight control. For teams with multiple sock types (e.g., thermal vs. moisture-wicking), signage and digital guidance help staff pick the right item for their job.
Adopt structured replacement strategies to control use:
- Scheduled Replacements: Based on known wear cycles
- Turn-in Systems: Require old socks before issuing new
- Time-based Allocations: Fixed quantities per month or quarter
Use tracking data to refine your stocking model over time. Adjust size ratios, order frequency, and safety stock levels based on real usage—not assumptions. The right balance ensures availability, reduces waste, and strengthens your procurement efficiency.
Cost-Benefit Analysis: Justifying Investment Decisions
For industrial buyers, justifying premium work boot sock purchases requires looking beyond unit price. A solid cost-benefit analysis highlights how higher-quality products reduce total spend and improve workforce outcomes.
Total Cost of Use
Durable work boot socks often last 2–3 times longer than basic versions. While the upfront cost may be higher, the cost per wear is significantly lower. Standardizing sock models also reduces complexity. Companies report fewer purchase orders, easier inventory tracking, and simplified reordering—cutting administrative time by up to 25%. For teams that stand or walk long hours, comfort improvements may reduce fatigue and breaks, indirectly improving productivity.
Waste control is another factor. Better sizing systems and usage protocols help avoid premature disposal or incorrect use. Reduced product waste means fewer reorders and less stockroom clutter.
Workforce Satisfaction and Retention
Comfortable PPE plays a major role in worker satisfaction—especially in high-turnover industries. Socks might seem small, but for physically demanding jobs, daily comfort matters. Employees often report fewer complaints and greater satisfaction when upgraded socks are provided, especially when included in onboarding kits or safety programs.
In competitive labor markets, offering comfort-oriented gear—even something as simple as quality socks—can set an employer apart. This also eliminates out-of-pocket costs for workers who otherwise purchase their own gear, improving perceived support for lower-wage roles. Turnover is expensive. Replacing one trained worker can cost 25–100% of their salary. If better socks help even slightly with retention, the return outweighs the initial investment.
Conclusion: Developing a Comprehensive Procurement Strategy
Effective work boot sock procurement requires strategic approaches that balance multiple considerations including performance requirements, economic factors, and implementation practicalities. Industrial organizations that implement comprehensive procurement strategies rather than transactional purchasing approaches typically achieve superior results across all these dimensions.
The business case for strategic work boot sock procurement remains compelling for most industrial operations, with the potential for both meaningful cost optimization through extended product lifespan and improved worker comfort contributing to productivity and satisfaction. The most successful programs typically share several characteristics: performance-based product selection aligned with specific application requirements, strategic supplier relationships that extend beyond basic transactions, appropriate inventory management systems ensuring product availability without excessive carrying costs, and comprehensive implementation planning that drives program acceptance and compliance.
For industrial procurement specialists developing or refining work boot sock programs, a phased implementation approach often proves most effective – beginning with thorough needs assessment and application mapping, proceeding through systematic supplier evaluation and product testing, implementing comprehensive rollout planning and worker education, and establishing regular review processes that drive continuous improvement based on both usage data and worker feedback. This measured approach reduces implementation challenges while allowing for program optimization based on actual experience and documented results. With strategic implementation and ongoing refinement, work boot sock programs can evolve from basic commodity purchases into valuable operational tools that enhance both worker experience and organizational performance.
FAQ: Common Questions About Work Boot Sock Procurement
What are the key differences between standard cotton work socks and performance work boot socks?
Performance socks use engineered fibers, targeted cushioning, and moisture-wicking features. They offer better durability, comfort, and foot protection—lasting 2–3 times longer than cotton socks despite higher initial cost.
How can work boot socks contribute to overall PPE program effectiveness?
High-quality socks enhance comfort, reduce foot fatigue, and prevent moisture-related issues, supporting the effectiveness of safety boots. They complement PPE by improving compliance, minimizing distractions, and lowering minor injury risks—especially in demanding environments with long standing hours or temperature extremes.
How should industrial operations determine appropriate replacement intervals for work boot socks?
Test socks under real-use conditions. Replace when cushioning compresses, fit loosens, or holes appear—typically after 30–50 washes. For daily wear, replace every 3–6 months; longer if rotated.
What are the most important performance features to evaluate when selecting work boot socks for industrial applications?
Key features include moisture control, cushioning, durability, fit, and temperature regulation. Prioritize moisture management and durability across all use cases; adapt other features to environment needs.
How can organizations calculate the return on investment for premium work boot sock programs?
Factor in product lifespan, lower replacement frequency, admin savings, reduced discomfort, and boot wear reduction. Most see 1.5–3× ROI within 6–12 months, depending on conditions and upgrade level.